Photocraft Encoders
Shaft Encoders
Shaft encoders are intended for direct coupling to a device shaft, and generate a specific pulse output for each revolution of the device shaft. To accommodate the angular and radial misalignment between the two shafts, we recommend a flexible shaft coupling or other similar technique.
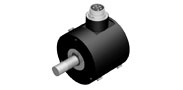
Hollow Shaft
Hollow shaft encoders are designed with either a through-bored shaft or a blind-bored shaft, and intended to mount directly onto a motor or other shaft. This eliminates the need for a shaft to shaft coupling and mounting adapter, resulting in both space and cost savings. The encoder “floats” on the motor shaft. A tether or flexible mounting bracket prevents the encoder from turning, yet accommodates shaft-to-shaft misalignment.
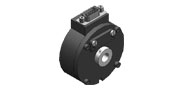
Wheeled Encoders
Wheeled encoders more accurately track the conveyor belt or other material than shaft encoders. Two problems with shaft encoders in this application are: (1) slippage of the conveyor belt on the roller, and (2) inaccuracy of roller diameters. Both of these contribute to inaccuracies that reduce the overall efficiency of a material handling sortation system or precision measuring system. Wheeled encoders ride directly on the moving material, use a wheel tread having a high coefficient of friction, and have a very low starting torque resulting in virtually no slippage of the wheels on the belt. In addition, the wheels are precision ground with exacting tolerances, versus a roller which has a much larger tolerance and its circumference seldom translates into an integral number of encoder pulses per unit of linear movement.
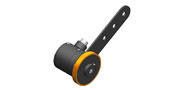
Programmable Encoders

Absolute Encoders
A single-turn, absolute encoder generates a multi-bit binary code word indicating the angular position of the shaft. Each equal sized segment of one shaft rotation is indicated by a unique value. When power is first applied the shaft position is immediately known without having to re-home, even if the shaft is moved when power is off.
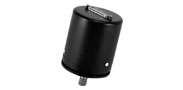
Accessories
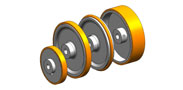